Jim Caprio1, Matt Ciarrocca1, Brian Rhoads1
1United Refractories Co., McMurray, PA, USA
Keywords: Iron, Steel, Refractory, Reheat Furnace, Rolling Mill
Abstract
There are many different types of reheat furnaces used by the steel industry to reheat slabs, blooms, billets, and other shapes. Each type of steel reheat furnace has its own set of technical refractory challenges to overcome in order for the reheat furnace to be efficient and operate smoothly. The goal of this paper is to identify the unique set of refractory challenges for each type of reheat furnace and offer product types that have been used successfully to address the challenges.
1. Introduction
The reheat furnace application is a critical part of the steel making process. Based on two different operations, continuous and batch, the reheat furnaces can vary in length, capacity, width, and thermal profile. Based on the furnace conditions, each will have a specific refractory design and configuration to maximize success. In addition, each reheat furnace will have specific technical refractory challenges to overcome in order to reach and operate at maximum efficiency. Once the refractory challenges are identified, a solution can be implemented.
Before discussing the technical refractory challenges to consider in steel reheat furnaces, it is important to understand the definition of refractory, the types of refractories, and the various methods that can be utilized to install refractories.
One definition of a refractory is an inorganic material that does not change chemically or physically when subjected to high temperatures and severe operating conditions.
When choosing the best refractory for a given application, it is important to consider what challenges are present. For example, does the refractory application have high abrasion issues or a large thermal profile variation (like can be seen in some reheat furnace hearths). Once the refractory technical challenges are known, it must then be decided what type of refractory should be chosen and what installation method is best to meet the need of the specific project (furnace conditions, timing, cost, goal of furnace life, etc.).
For steel reheat furnaces, monolithic refractories are an excellent choice. What is a monolithic refractory? A monolithic refractory is an unshaped refractory (versus a fired brick that is a “shaped” refractory) that forms a relatively joint-free monolithic lining. Monolithic refractories for reheat furnaces are a mixture of refractory grains of different sizes, fine powders, and a bond system. When mixed with the correct liquid additive, the monolithic refractory is used to form a relatively joint-free refractory lining. The installation of monolithic refractories is usually more efficient and faster than relining or constructing a new reheat furnace versus brick installations. When the appropriate, state-of-the-art monolithic refractory is specified, the physical properties will be equal to or better than the properties of brick.
There are four (4) main types of monolithic refractories that are used in reheat furnaces. The types include cast, shotcrete, gunning, and plastic. Each type has specific advantages and disadvantages which should be considered when picking one over another.
1.1. Cast – Under this monolithic type, there are four (4) types of cast products as follows:
1.1.1. Hand Cast – mixed castable is poured, dumped, or shoveled into place. This installation method is usually the easiest and least expensive to install, however, the disadvantages include usually higher water content and reduced physical properties.
1.1.2. Vibration Cast – mixed castable is vibrated into place while air is being removed from the material due to the vibration of the mix. This installation method usually uses lower water content and optimizes properties. The disadvantages include vibration equipment is required and physical properties can fluctuate based on too much or too little vibration.
1.1.3. Pump Cast – mixed castable is pumped through a hose to where the material is being installed into forms. This installation method allows material to be transferred quickly from the mixer to the forms being filled and a large area can be installed without having to move the mixer and pump. The disadvantages are that a pump and hoses are required and that some installers can add too much liquid to the material being pumped.
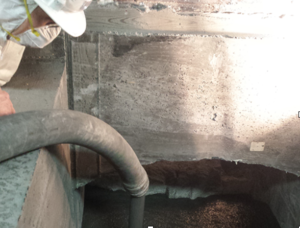
1.1.4. Self-Flow – mixed castable flows into place without the need of a vibrator or pump. This installation method usually requires lower labor and allows the material to fill the forms easily. The disadvantages are the mix usually costs more as it is a more complex mix, there may be reduced properties due to high water content, and more robust forms are needed for some applications.
1.2. Shotcrete – this is a “wet” process where the mixed castable is pumped through a hose and is shot in place without the need for forms. This is done by adding an activator and compressed air at the nozzle. This type of installation is fast and usually reduces the furnace downtime. The disadvantages are special equipment is needed, the pump and nozzle operators are key to the success of the installation, and the rebound material is not reusable.
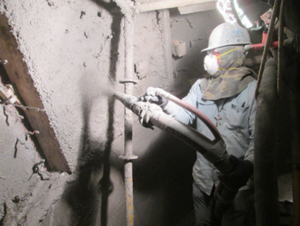
1.3. Gunning – this is a “dry” process where dry gun mix is transferred to the nozzle using a rotary valve gun and compressed air, then is gunned in place without the need for forms. This is done by adding a liquid at the nozzle to the dry gun mix so the now wet mix sticks to wherever it is being applied. This installation method requires minimal equipment, is fast to set-up, not complicated, and is very good for quick repairs to get a furnace up and running. The disadvantages are reduced properties if too much liquid is added at the nozzle and usually higher rebounds versus shotcreting. There are some specially designed gunning nozzles that minimize dusting and rebound.
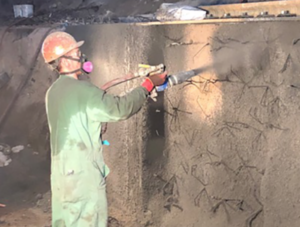
1.4. Plastic – a wet refractory mass that is usually supplied in slabs in a raw and unfired state. These refractory slabs are rammed with an air hammer, or beaten into place, so it is labor-intensive. The rammed plastic is ready to be heated as soon as it is installed. However, it must be heated slowly to remove water, but it is not nearly as “sensitive” as a castable during dry out. Plastic refractory is an excellent choice for fast repairs & quick turnarounds.
2. Types of Reheat Furnaces
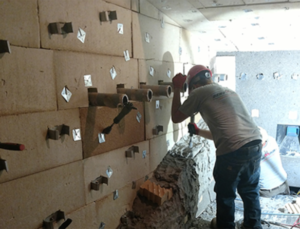
2.1. Continuous Operation Reheat Furnaces
2.1.1. Walking Beam
2.1.2. Pusher
2.1.3. Rotary Hearth
2.2 Batch Reheat Furnace
2.2.1. Car Bottom
2.2.2. Stationary Solid Hearth
3. Specific Refractory Technical Challenges
3.1. Walking Beam Reheat Furnace – in a walking beam reheat furnace, three main technical challenges to address include scale build-up, high temperature hot strength requirements, and thermal profile variations.
3.2. Pusher Reheat Furnace – in a pusher reheat furnace, three main technical challenges to address include high abrasion, high temperature hot strength requirements, and thermal profile variations.
3.3. Rotary Hearth Reheat Furnace – in a rotary hearth reheat furnace, two main technical challenges to address include high abrasion and high temperature hot strength requirements.
3.4. Car Bottom Reheat Furnace – in a car bottom reheat furnace, three main technical challenges to address include thermal cycling, high temperature hot strength requirements of the car deck, and the thermal profile of the roof and upper sidewalls.
3.5. Stationary Solid Hearth Furnace – in a stationary solid hearth furnace, three main technical challenges to address include thermal cycling, high temperature hot strength requirements, and abrasion resistance.
4. Product Types to Address the Refractory Technical Challenges
4.1. Continuous Operation Reheat Furnaces
For continuous operation reheat furnaces, including walking beam, pusher, and rotary hearth, the following product types have been used successfully in the different areas to allow the reheat furnaces to operate at maximize efficiency.
4.1.1. Burners Walls and Side Walls – High alumina pumpables and shotcretes with high hot strength and thermal shock resistance work best. Plastic refractories, both phosphate-bonded and air set, designed with good hot strength and volume stability also work well in these areas.
4.1.2. Wall Back-Up Insulation – A 960–1280 kg/m3 lightweight insulation castable or gun mix works well as a back-up lining to the working face.
4.1.3. Burner Surround – A high alumina, phosphate-bonded, plastic refractory with high hot strength and good abrasion resistance works well.
4.1.4 Roof – High alumina pumpables and shotcretes with high hot strength and thermal shock resistance work best. UltraBloc panels also work well in some furnaces. UltraBloc custom engineered panels are manufactured with extremely high-compression ceramic fiber and minimal joints. With a high tensile strength, low thermal conductivity, and the ability to withstand temperatures up to 3000ºF, UltraBloc Panels are perfect for use in reheat furnaces.
4.1.5. Roof Back-Up Insulation – A 560-960 kg/m3 lightweight insulation castable or gun mix works well as a back-up lining to the roof working lining.
4.1.6. Hearth – High alumina pumpables with high hot strength good abrasion resistance and good thermal shock resistance work best.
4.1.7. Hearth Back-Up Insulation – A lightweight castable in the 960-2,080 kg/m3 range with good strength has worked best in this area.
4.1.8. Pusher & Skid Blocks – A high alumina, spinel enriched, low cement castable designed with high hot strength works well in these areas.
4.1.9. Charge and Discharge Doors – A lightweight castable with high strength and a medium density high alumina pumpable both perform well in these areas. UltraBloc panels also work well in some furnaces.
4.1.10. Repair Products – A high alumina, low cement, gun mix designed with rapid-fire technology, good abrasion resistance, and minimal rebound has worked well to repair skids, posts, and other areas of the furnace for additional furnace life.
4.2. Batch Operation Reheat Furnaces
For batch operation reheat furnaces, including car bottom and stationary solid hearth, the following product types have been used successfully in the different areas to allow the reheat furnaces to operate at maximize efficiency.
4.2.1. Car Bottoms and Hearths – High alumina pumpables with high hot strength good abrasion resistance and good thermal shock resistance work best.
4.2.2. Subhearth – Lightweight castables in the 1,280-1,760 kg/m3 range with good strength have worked best in this area.
4.2.3. Roofs – UltraBloc panels work well in this area. UltraBloc custom engineered panels are manufactured with extremely high-compression ceramic fiber and minimal joints. With a high tensile strength, low thermal conductivity, and the ability to withstand temperatures up to 1650ºC, UltraBloc Panels are perfect for use in reheat furnaces.
4.2.4. Upper Side Walls – Log Modules work very well in this area. Log Modules are ceramic fiber manufactured to full furnace lining thickness & are designed to eliminate the joints & shrinkage commonly associated with standard module furnace wall designs. Each log module is continuously folded to the custom length requirements and compressed to specific density utilizing compression & banding system. The log modules are installed with an external anchoring system which allows for maximum weld quality during installation. The end result are linings with low heat loss which increases the overall furnace efficiency.
4.2.5. Lower Side Walls – High alumina pumpables and shotcretes with high hot strength and thermal shock resistance work best. Phosphate-bonded plastic refractories designed with good hot strength and volume stability also work well in these areas.
4.2.6. Jambs – Phosphate-bonded plastic refractories designed with good hot strength and volume stability work well in this area.
4.2.7. Doors – UltraBloc works well in this area.
5. General Summary of Product Types
Table 1. General Summary of Product Types
5.1. Rapid Fire (RF) Technology
For some of the product types listed above, Rapid Fire (RF) Technology is available. RF Technology allows the lining to be fired faster than a typical firing schedule. For example, in a single-component lining that is 225mm or less, the typical firing schedule may be up to 70 hours. With RF Technology, the firing schedule would be reduced to approximately 24 hours.
6. Product Success Stories
6.1.Continuous Operation Reheat Furnaces
6.1.1. Walking Beam
A 60% alumina pump mix with high hot strength, good abrasion resistance, and good thermal shock resistance was used for hearth and wall reline in a walking beam reheat furnace for carbon steel slabs. This product was utilized in various areas of the furnace as it could be both pump cast and shotcrete. The hearth and roof sections were pump cast and the sidewalls and burner walls were shotcrete. The versatility of this high alumina pump mix allowed the reheat furnace to be relined in a minimal amount of time as one product was ordered, so the installation crew did not have to worry about multiple products on the jobsite.
A 60% alumina, low cement, gun mix designed with rapid-fire technology, good abrasion resistance, and minimal rebound was used to repair skid pipes & stationary posts in a walking beam reheat furnace for carbon steel slabs. This product was also used for some veneer repairs. During the repair the gun mix was applied using a specially designed nozzle system which allowed the product to have minimum rebound, improved density, and improved hot strengths.
6.1.2. Rotary Hearth Furnace
A cement-free 60% alumina shotcrete mix with high hot strength, good abrasion resistance, and good thermal shock resistance was used to reline the inner and outer side walls of a rotary hearth furnace that was reheating pipe. This product was a cement-free single component mix, dry gel system in mix (no colloidal silica) & activated at the nozzle with an accelerator. Advantages were quick installation, minimal labor (versus pumping into a form), rapid furnace dry out, and excellent hot strengths.
6.2. Batch Type Furnaces
6.2.1. Car Bottom Reheat Furnace
Utilizing a URC engineered furnace kit for a car bottom reheat furnace that heated ingots being forged into rolls, a customer’s furnace was down for a minimal amount of time because of the streamlined approach for obtaining all of the furnace components. URC’s engineered furnace kit utilizes a combination of precast shapes for lower side walls, jambs, and lintels, an UltraBloc roof system, a log module upper sidewall design, and a combination of a high alumina pump mix and lightweight pump mix for car decks to be installed in place.
6.2.2. Solid Hearth Box Type Furnace
Customer had a solid hearth box furnace they needed repaired for improved efficiency in heating up carbon steel billets. UltraBloc panels were utilized for all sidewalls, backwalls, and roof section. The hearth was completed using a combination of precast shapes and a high alumina pump mix with high hot strength, good abrasion resistance, and good thermal shock resistance. The jambs were rammed with a phosphate-bonded high alumina plastic and the doors were completed using an UltraBloc panel design.
7. Conclusion
There are many technical refractory challenges that may present themselves during the life of a reheat furnace. By understanding these challenges and the refractory solutions that are available, it is possible to get a reheat furnace back to where it is efficient and operating smoothly. When understanding the different types of monolithic refractories available and the corresponding installation methods, the refractory design becomes even better as the right questions will be asked and the correct refractory solution will be implemented in your reheat furnace.